




Car grille ABS shell
The ABS shell of the car's grille is an important component of the vehicle's front face. It not only serves an aesthetic purpose but also plays a role in protecting the internal structure of the vehicle and guiding airflow into the engine compartment.
Email:
The ABS shell of the car grille is an important component of the car's front face. It not only serves an aesthetic purpose but also protects the internal structure of the vehicle and guides airflow into the engine compartment. Below is a detailed analysis of the ABS shell of the car grille.
1. Characteristics of ABS Material
ABS (Acrylonitrile-Butadiene-Styrene Copolymer) is a thermoplastic material with excellent physical properties and chemical stability, making it one of the ideal materials for car grille shells. Its main characteristics include:
Impact Resistance: ABS material has high impact strength, effectively resisting external impacts and protecting the car's front from damage.
Rigidity: ABS material has a certain degree of rigidity, allowing it to maintain the shape and stability of the car grille.
Oil Resistance: ABS material has good corrosion resistance to chemicals such as grease, helping to keep the shell clean and aesthetically pleasing.
Cold Resistance: ABS material maintains good performance at low temperatures, making it less prone to brittleness or deformation.
Ease of Processing: ABS material is easy to mold and process, allowing for the production of various shapes and sizes of car grille shells.
2. Design of Car Grille ABS Shell
The design of the car grille ABS shell needs to consider multiple factors, including the overall style of the vehicle, intake efficiency, heat dissipation performance, and safety. The design process typically follows these principles:
Aesthetics: The design of the shell should coordinate with the overall style of the vehicle, enhancing its visual effect.
Functionality: The shell should effectively guide airflow into the engine compartment, improve intake efficiency, and ensure good heat dissipation performance.
Safety: The shell should have a certain strength and rigidity to protect the internal structure of the vehicle and passenger safety in case of a collision.
Ease of Maintenance: The design of the shell should facilitate cleaning and maintenance, reducing usage costs.
3. Manufacturing Process
The manufacturing process for car grille ABS shells typically includes injection molding, extrusion molding, etc. Among these, injection molding is one of the most commonly used manufacturing processes. During injection molding, ABS material is heated to a molten state and then injected into a mold to form. The design of the mold should consider factors such as the shape, size, and precision of the shell. After forming, post-processing is also required, such as trimming burrs and removing gates.
4. Maintenance and Care
To extend the service life of the car grille ABS shell and maintain its performance, regular maintenance and care are necessary. Here are some suggestions:
Regular Cleaning: Use a soft cloth or specialized cleaner to wipe the surface of the shell to remove dust and dirt. Avoid using corrosive cleaners or sharp objects to scratch the shell.
Check Fixing Condition: Regularly check the fixing condition of the shell to ensure that its connection with the body is firm and reliable.
Avoid Impacts: Avoid heavy objects striking the shell to prevent damage or deformation.
Regularly Check for Damage: Regularly inspect the shell for cracks, deformation, or damage; if found, replace it promptly.
In summary, car grille ABS shells have excellent performance and broad application prospects. During design and manufacturing processes, it is essential to fully consider material characteristics, overall vehicle style, and user needs to ensure that the quality and performance of the shell meet requirements. Additionally, regular maintenance and care are key to maintaining shell performance and extending its service life.
Classification:
Automotive injection molds
Key words:
Household Appliances
Auto Parts
Medical Equipment
Deep branch in dongguan mould
Integration of mold manufacturing and molding production
ADVANTAGES
Development team adhering to the "customer first" service consciousness, relying on a strong professional knowledge and high quality expert team will develop its own position to provide customers with injection molding, mold development, customized one-stop service, meet customer's various customization development demand of professional team, to provide comprehensive solutions to the customers
01
Mold development, design and manufacture
Engineering development technical team size: 30 people.
02
Advanced modern precision mold equipment
62 high precision mold production equipment, the scale of 80 people.
03
Injection molding production
94 sets of injection molding equipment and 240 production personnel.
04
Product high quality testing equipment
Systematic quality management team of 30 people, advanced testing equipment: physical tester, life tester, high precision inspection size tester, etc
STANDARDIZED PROCESSING FLOW
Relying on strong professional knowledge and a high-quality expert team, we provide customers with customized one-stop services for injection molding and mold development
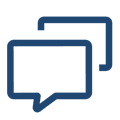
Demand Communication

01
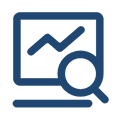
feasibility analysis

02
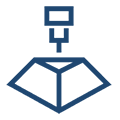
mold design

03
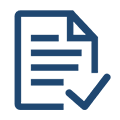
Customer Confirmation

04
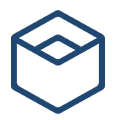
Mold manufacturing

05
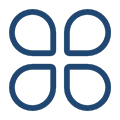
Sample delivery

06
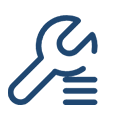
Internal optimization

07
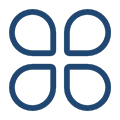
Sample delivery

08
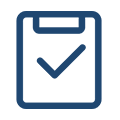
Customer Confirmation

09
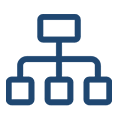
Mass production

10
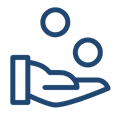
After-sales tracking

11
MORE PRODUCTS
PRODUCT CONSULTING
* Note: Please fill in the information accurately so as to facilitate smooth communication. We will contact you as soon as possible.