

Plastic shell scissors
Basic Definition and Material Plastic shell scissors are cutting tools with a plastic outer shell and metal blades. Common plastic materials for the shell include acrylonitrile-butadiene-styrene copolymer (ABS) and polycarbonate (PC). ABS plastic has good overall performance, such as high toughness and ease of processing, making the scissor shell sturdy and durable while being easy to produce; PC plastic is known for its excellent impact resistance and heat resistance, ensuring the stability of the scissors in various environments. Significant Features: Lightweight and Portable: The low density of plastic significantly reduces the weight of plastic shell scissors compared to all-metal scissors, making them easy to carry. Whether for daily household storage and organization or for use while traveling or at the office, they won't become a burden. Safe and Comfortable: The relatively soft texture of the plastic shell reduces the risk of injury from accidental collisions during use. Additionally, through ergonomic design, the plastic shell can create grips that fit the hand better, making it less tiring to use for extended periods. Variety of Colors: Plastic is easy to dye, allowing for the production of various bright and rich colors to meet different consumers' aesthetic needs, adding a touch of fashion to the home and making it easy to find among many tools. Manufacturing Process: Injection Molding: Melted plastic is injected into specific mold cavities, and after cooling and solidifying, it forms scissors shells with precise shapes. This process efficiently produces complex-shaped shell components, ensuring product consistency and accuracy. Assembly Process: After the shell is formed, the carefully polished metal blades are assembled with the plastic shell, ensuring smooth opening and closing of the blades and uniform cutting force, achieving good cutting functionality. Applicable Scenarios: Daily Household: Suitable for cutting paper, fabric, food packaging bags, and various household items, easily handling various cutting needs at home. Office Scenarios: For handling documents, envelopes, labels, and other office supplies, compact and lightweight, taking up little space, making them a reliable assistant on the desk. Handicrafts: For craft enthusiasts, plastic shell scissors, with their rich colors and comfortable grip, become ideal tools for activities like paper cutting, origami, and fabric crafts. Children's Use: Due to their lightweight and safe characteristics, specially designed children's plastic shell scissors are great helpers for kids learning crafts and drawing, helping to develop their hands-on skills. Environmental Considerations: Discarded plastic shell scissors can be processed through recycling channels. Some plastic materials can be recycled and reused, going through sorting, cleaning, crushing, and re-pelletizing processes, and re-entering the production of plastic products, achieving resource recycling and reducing pressure on the environment.
Email:
Basic Definition and Material
Plastic shell scissors are cutting tools with a plastic outer shell and metal blades. Common plastic materials for the shell include acrylonitrile-butadiene-styrene copolymer (ABS) and polycarbonate (PC). ABS plastic has good overall performance, such as high toughness and ease of processing, making the scissors' shell sturdy and durable while being easy to produce; PC plastic is known for its excellent impact resistance and heat resistance, ensuring the scissors' stability in various environments.
Significant Features:
- Lightweight and PortableThe low density of plastic material significantly reduces the weight compared to all-metal scissors, making plastic shell scissors easy to carry. Whether for daily household storage and organization or for use while traveling or at the office, they won't become a burden.
- Safe and ComfortableThe plastic shell is relatively soft, reducing the risk of injury from accidental collisions during use. Additionally, through ergonomic design, the plastic shell can create grips that fit the hand better, making it less tiring to use for extended periods.
- Diverse ColorsPlastic is easy to dye, allowing for the production of various bright and rich colors to meet different consumers' aesthetic needs, adding a touch of fashion to the home and making it easy to find among many tools.
Manufacturing Process:
- Injection MoldingThis process involves injecting molten plastic into a specific mold cavity, which cools and solidifies to form a precisely shaped scissors shell. This technique efficiently produces complex-shaped shell components, ensuring product consistency and accuracy.
- Assembly ProcessAfter the shell is formed, the carefully polished metal blade is assembled with the plastic shell, ensuring smooth opening and closing of the blade and uniform cutting force, achieving good cutting functionality.
Applicable Scenarios
- Daily Household UseSuitable for cutting paper, fabric, food packaging bags, and various household items, easily meeting various cutting needs at home.
- Office ScenariosUsed for handling documents, envelopes, labels, and other office supplies, compact and lightweight, taking up little space, making it a reliable assistant on the desk.
- HandicraftsFor craft enthusiasts, plastic shell scissors, with their rich colors and comfortable grip, are ideal tools for activities like paper cutting, origami, and fabric crafts.
- Children's UseDue to their lightweight and safe characteristics, specially designed children's plastic shell scissors are great helpers for kids learning crafts and drawing, helping to develop their hands-on skills.
Environmental Considerations:
Discarded plastic shell scissors can be processed through recycling channels. Some plastic materials can be recycled and reused, going through sorting, cleaning, crushing, and re-pelletizing processes to be reintegrated into the production of plastic products, achieving resource recycling and reducing environmental pressure.
Classification:
Other injection molds
Key words:
Integration of mold manufacturing and molding production
ADVANTAGES
Development team adhering to the "customer first" service consciousness, relying on a strong professional knowledge and high quality expert team will develop its own position to provide customers with injection molding, mold development, customized one-stop service, meet customer's various customization development demand of professional team, to provide comprehensive solutions to the customers
01
Mold development, design and manufacture
Engineering development technical team size: 30 people.
02
Advanced modern precision mold equipment
62 high precision mold production equipment, the scale of 80 people.
03
Injection molding production
94 sets of injection molding equipment and 240 production personnel.
04
Product high quality testing equipment
Systematic quality management team of 30 people, advanced testing equipment: physical tester, life tester, high precision inspection size tester, etc
STANDARDIZED PROCESSING FLOW
Relying on strong professional knowledge and a high-quality expert team, we provide customers with customized one-stop services for injection molding and mold development
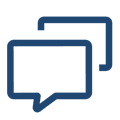
Demand Communication

01
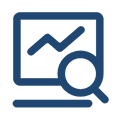
feasibility analysis

02
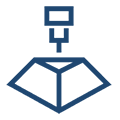
mold design

03
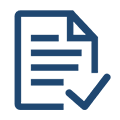
Customer Confirmation

04
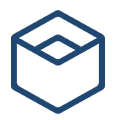
Mold manufacturing

05
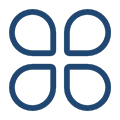
Sample delivery

06
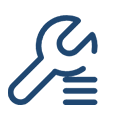
Internal optimization

07
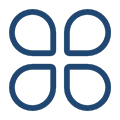
Sample delivery

08
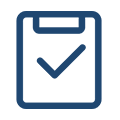
Customer Confirmation

09
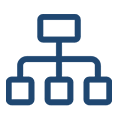
Mass production

10
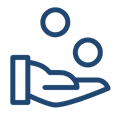
After-sales tracking

11
MORE PRODUCTS
PRODUCT CONSULTING
* Note: Please fill in the information accurately so as to facilitate smooth communication. We will contact you as soon as possible.