


Plastic casing for electronic appliances
Plastic housings for electronic and electrical devices play a crucial role in electronic and electrical equipment. They not only protect internal circuits and components from external environmental damage but also affect the product's appearance, feel, and user experience.
Email:
The plastic shells of electronic and electrical appliances play a crucial role in electronic and electrical devices. They not only protect internal circuits and components from external environmental damage but also affect the product's appearance, feel, and user experience. The following is a detailed analysis of the plastic shells of electronic and electrical appliances:
1. Material Selection
The materials for plastic shells of electronic and electrical appliances are diverse, commonly including ABS, PP, PC, HIPS, etc. These materials are widely used in the manufacturing of electronic and electrical shells due to their unique physical and chemical properties.
ABS (Acrylonitrile-Butadiene-Styrene Copolymer): ABS plastic has a wide range of raw material sources, is easy to mold and process, and has excellent impact resistance, making it an important material in the manufacturing of household appliance shells. It is widely used in the production of shells for various electrical products such as televisions, washing machines, refrigerators, and computers.
PP (Polypropylene): PP plastic is lightweight, has high specific strength, is corrosion-resistant, has good insulation properties, and low processing costs, making it widely used in the manufacturing of appliance shells. Especially in some small appliances that require high heat resistance, modified PP has become an ideal choice.
PC (Polycarbonate): PC plastic has extremely high toughness, impact strength, and transparency, making it outstanding in the manufacturing of household appliance shells, especially those requiring high transparency and high-temperature resistance. For example, PC plastic is widely used in the production of shells for high-end water dispensers and water heaters.
HIPS (High Impact Polystyrene): HIPS plastic also has good impact resistance and processing performance and is commonly used in the manufacturing of appliance shells that do not require high strength.
2. Design and Manufacturing
Design Principles: The design of electronic and electrical plastic shells should follow the principle of combining functionality with aesthetics. While protecting internal circuits and components, the design of the shell should also consider the product's appearance, feel, and user experience. For example, the shape, lines, and color of the shell can all affect the overall visual effect of the product.
Manufacturing Process: Injection molding is a common method for producing plastic shells for electronic appliances. It mainly involves injecting molten plastic material into a mold, then cooling and solidifying to obtain the desired shell shape. The injection molding process can produce electronic shells with complex shapes and fine structures, suitable for mass production.
Post-processing: The shells produced by injection molding usually require post-processing steps such as trimming burrs, removing gates, painting, etc. These post-processing steps can improve the surface quality and aesthetics of the shell.
3. Applications and Trends
Application Fields: Plastic shells for electronic appliances are widely used in various electronic and electrical devices such as televisions, washing machines, refrigerators, computers, mobile phones, small household appliances, etc. These shells not only protect internal circuits and components but also enhance product aesthetics and improve user experience.
Development Trends: With technological advancements and changing consumer demands, the manufacturing technology and design concepts for plastic shells of electronic appliances are continuously innovating. For example, using environmentally friendly materials, improving shell strength and toughness, optimizing heat dissipation performance have become current development trends. At the same time, intelligent and personalized designs have also become important development directions for plastic shells of electronic appliances.
4. Maintenance and Care
To extend the lifespan of plastic shells for electronic appliances and maintain their performance, regular maintenance and care are necessary. Here are some suggestions:
Avoid Impact: Avoid heavy objects striking the shell to prevent damage or deformation.
Keep Clean: Regularly clean the surface of the shell to remove dust and dirt. Use a soft damp cloth for wiping; avoid using corrosive cleaners or sharp objects to scratch the shell.
Pay Attention to Usage Environment: Avoid exposing electronic appliance products to extreme temperatures or humid environments to prevent affecting shell performance and lifespan.
In summary, plastic shells for electronic appliances play an important role in electronic and electrical devices. Choosing suitable materials, following design principles, adopting advanced manufacturing processes, and focusing on maintenance are key to ensuring shell quality and performance.
Classification:
Household appliance injection molds
Key words:
Household Appliances
Auto Parts
Medical Equipment
Deep branch in dongguan mould
Integration of mold manufacturing and molding production
ADVANTAGES
Development team adhering to the "customer first" service consciousness, relying on a strong professional knowledge and high quality expert team will develop its own position to provide customers with injection molding, mold development, customized one-stop service, meet customer's various customization development demand of professional team, to provide comprehensive solutions to the customers
01
Mold development, design and manufacture
Engineering development technical team size: 30 people.
02
Advanced modern precision mold equipment
62 high precision mold production equipment, the scale of 80 people.
03
Injection molding production
94 sets of injection molding equipment and 240 production personnel.
04
Product high quality testing equipment
Systematic quality management team of 30 people, advanced testing equipment: physical tester, life tester, high precision inspection size tester, etc
STANDARDIZED PROCESSING FLOW
Relying on strong professional knowledge and a high-quality expert team, we provide customers with customized one-stop services for injection molding and mold development
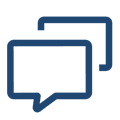
Demand Communication

01
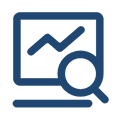
feasibility analysis

02
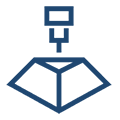
mold design

03
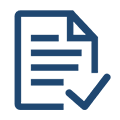
Customer Confirmation

04
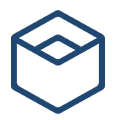
Mold manufacturing

05
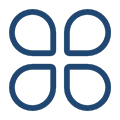
Sample delivery

06
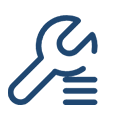
Internal optimization

07
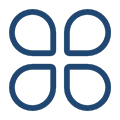
Sample delivery

08
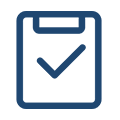
Customer Confirmation

09
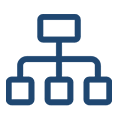
Mass production

10
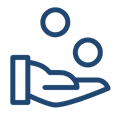
After-sales tracking

11
MORE PRODUCTS
PRODUCT CONSULTING
* Note: Please fill in the information accurately so as to facilitate smooth communication. We will contact you as soon as possible.