




Plastic casing for medical device equipment
The plastic shell of the shaping and slimming machine is an important component. It not only protects the internal mechanical structure and electronic components but also affects the overall appearance of the product and the user experience.
Email:
The plastic shell of the shaping and slimming machine is an important component. It not only protects the internal mechanical structure and electronic components but also affects the overall appearance and user experience of the product. Below is a detailed analysis of the plastic shell of the shaping and slimming machine:
1. Material Selection
The plastic shell of the shaping and slimming machine is usually made of materials such as ABS and fiberglass.
ABS Material:
Advantages: ABS material is lightweight, high-strength, corrosion-resistant, and easy to process and mold. It also has a good balance of toughness and hardness, allowing it to withstand impacts and pressure during daily use.
Application: ABS material is widely used in the manufacturing of various shaping and slimming machine shells, such as massagers and fitness devices.
Fiberglass Material:
Advantages: Fiberglass material is composed of glass fibers and epoxy resin, featuring lightweight, high strength, wear resistance, and corrosion resistance.
Disadvantages: The toughness of fiberglass material is not strong, making it unsuitable for products that need to be reassembled. Additionally, it is not environmentally friendly, causes significant pollution, and has a strong odor during production that can be harmful to humans.
Application: Due to the aforementioned disadvantages of fiberglass material, its application in the manufacturing of shaping and slimming machine shells is relatively limited.
2. Design and Manufacturing
Design Principles:
Functionality: The shell design should ensure protection for internal mechanical structures and electronic components while being convenient for user operation and portability.
Aesthetics: The lines, shapes, and colors of the shell should match the overall style of the product to enhance its aesthetic appeal.
Durability: The shell should have sufficient strength and durability to withstand impacts and pressure during daily use.
Manufacturing Process:
Injection Molding: Melted plastic material is injected into a mold, cooled, and solidified to form the desired shape of the shell. The injection molding process has advantages such as high production efficiency, low cost, and the ability to produce complex shapes.
Vacuum Forming: Particularly suitable for manufacturing large-area, complex-shaped shells. Thick sheet vacuum forming technology softens plastic sheets through heating, then adheres them to the mold surface before cooling and solidifying to form the desired shape.
Post-Processing:
Spraying: To enhance the aesthetics and corrosion resistance of the shell, spraying treatment is usually required. Spraying materials can include paint or powder coatings.
Silk Screen Printing: Printing text, patterns, or other identification information on the shell to improve product recognition and aesthetics.
3. Features and Advantages
Lightweight and High Strength: The plastic shell is characterized by being lightweight yet strong, making it easy for users to carry and use.
Corrosion Resistance: Plastic materials have good corrosion resistance, able to withstand chemical corrosion and physical wear during daily use.
Easy to Process and Mold: Plastic materials are easy to process into various shapes and sizes for shells that meet different product needs.
High Aesthetic Appeal: Plastic shells can be beautified through processes like spraying or silk screen printing to enhance the overall aesthetic quality of the product.
4. Maintenance and Care
To extend the lifespan of the plastic shell of the shaping and slimming machine and maintain its performance, regular maintenance and care are necessary. Here are some suggestions:
Avoid Impacts: Prevent heavy objects from striking the shell to avoid damage or deformation.
Keep Clean: Regularly clean the surface of the shell to remove dust and dirt. Use a soft damp cloth for wiping; avoid using corrosive cleaners or sharp objects that could scratch the shell.
Avoid High Temperatures: Avoid exposing the shaping and slimming machine to high-temperature environments to prevent affecting the performance and lifespan of the shell.
In summary, the plastic shell of the shaping and slimming machine has specific characteristics and requirements in terms of material selection, design and manufacturing, features and advantages, as well as maintenance and care. Through reasonable material selection, design manufacturing, and maintenance care, we can ensure the quality and performance of the shell while enhancing overall product quality and user experience.
Classification:
Medical injection molds
Key words:
Household Appliances
Auto Parts
Medical Equipment
Deep branch in dongguan mould
Integration of mold manufacturing and molding production
ADVANTAGES
Development team adhering to the "customer first" service consciousness, relying on a strong professional knowledge and high quality expert team will develop its own position to provide customers with injection molding, mold development, customized one-stop service, meet customer's various customization development demand of professional team, to provide comprehensive solutions to the customers
01
Mold development, design and manufacture
Engineering development technical team size: 30 people.
02
Advanced modern precision mold equipment
62 high precision mold production equipment, the scale of 80 people.
03
Injection molding production
94 sets of injection molding equipment and 240 production personnel.
04
Product high quality testing equipment
Systematic quality management team of 30 people, advanced testing equipment: physical tester, life tester, high precision inspection size tester, etc
STANDARDIZED PROCESSING FLOW
Relying on strong professional knowledge and a high-quality expert team, we provide customers with customized one-stop services for injection molding and mold development
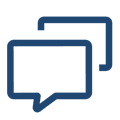
Demand Communication

01
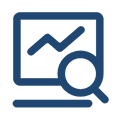
feasibility analysis

02
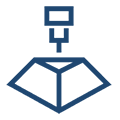
mold design

03
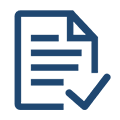
Customer Confirmation

04
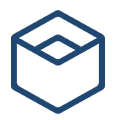
Mold manufacturing

05
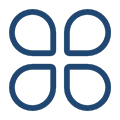
Sample delivery

06
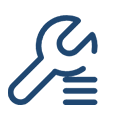
Internal optimization

07
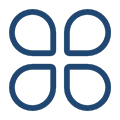
Sample delivery

08
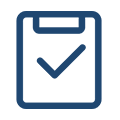
Customer Confirmation

09
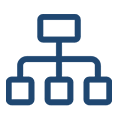
Mass production

10
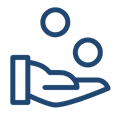
After-sales tracking

11
MORE PRODUCTS
PRODUCT CONSULTING
* Note: Please fill in the information accurately so as to facilitate smooth communication. We will contact you as soon as possible.