



Outdoor storage power supply shell for mobile power bank
The shell of the portable power bank for outdoor energy storage is an important part that protects the internal battery pack and electronic components, while also affecting the product's portability, durability, and overall appearance.
Email:
The shell of the outdoor energy storage power bank is an important part that protects the internal battery pack and electronic components, while also affecting the product's portability, durability, and overall appearance. Below is a detailed introduction to the shell of the outdoor energy storage power bank:
1. Material Selection
Aluminum Alloy: The aluminum alloy shell is lightweight, high-strength, corrosion-resistant, and has excellent heat dissipation properties, making it very suitable for outdoor environments. In addition, aluminum alloy can enhance the product's texture and aesthetics.
ABS Engineering Plastic: ABS engineering plastic has good wear resistance and impact resistance, and is relatively low in cost. It is suitable for various outdoor environments and can withstand certain impacts and vibrations.
2. Design Features
Portability: The design of the outdoor energy storage power bank shell should fully consider portability by optimizing size and weight, allowing users to carry it easily. For example, a modular design can allow users to replace or expand battery modules according to their needs, increasing the product's flexibility and making it easier to carry and store.
Durability: The shell material must have high strength, corrosion resistance, waterproofing, and dustproof characteristics. Common structural designs include reinforcing ribs and cushioning layers to improve product durability. At the same time, the shell should have certain waterproofing and dustproof capabilities to ensure stable operation of the device under different climatic conditions.
Safety: The shell design must ensure user safety in various usage scenarios. Fireproof and explosion-proof features can prevent internal battery short circuits or overheating from causing fires or explosions. Electric shock prevention designs can ensure that users do not come into contact with live components during use by adding insulation layers and designing reasonable protective structures.
3. Production Process
Injection Molding: Melted plastic is injected into a mold, and after maintaining pressure and cooling, a formed shell is obtained. Injection molding has advantages such as high production efficiency, low cost, and strong adaptability.
Blow Molding: Suitable for producing complex-shaped and larger-sized shells. Through blow molding technology, plastic can be blown into the desired shape.
4. Color and Personalization
Color Matching: The color selection of the shell should balance practicality and aesthetics. Neutral tones such as black, white, and gray are more common as they are easier to match with various usage scenarios. At the same time, limited colors or special editions can be considered to increase the product's market appeal.
Personalized Design: Through unique shapes and innovative detail processing methods, each mobile power outdoor energy storage power bank can become an extension of the user's personality, meeting different users' aesthetic needs.
5. Maintenance and Care
Regular Cleaning: Use a soft damp cloth to wipe the surface of the shell to remove dust and stains. Avoid using corrosive cleaners or sharp objects to scratch the shell.
Avoid Drops and Impacts: Although the shell has certain impact resistance, long-term drops and impacts may still lead to shell damage or internal component damage. Therefore, efforts should be made to avoid drops and impacts during use.
Waterproofing and Dustproofing: When used outdoors, ensure that the shell has good waterproofing and dustproofing performance. Avoid exposing the power bank to damp or dusty environments for extended periods.
In summary, the design and production of the outdoor energy storage power bank shell need to comprehensively consider multiple aspects such as material, portability, durability, safety, production process, color and personalization, as well as maintenance and care. Through reasonable design and production processes, it is possible to produce a beautiful yet practical outdoor energy storage power bank shell.
Classification:
Household appliance injection molds
Key words:
Household Appliances
Auto Parts
Medical Equipment
Deep branch in dongguan mould
Integration of mold manufacturing and molding production
ADVANTAGES
Development team adhering to the "customer first" service consciousness, relying on a strong professional knowledge and high quality expert team will develop its own position to provide customers with injection molding, mold development, customized one-stop service, meet customer's various customization development demand of professional team, to provide comprehensive solutions to the customers
01
Mold development, design and manufacture
Engineering development technical team size: 30 people.
02
Advanced modern precision mold equipment
62 high precision mold production equipment, the scale of 80 people.
03
Injection molding production
94 sets of injection molding equipment and 240 production personnel.
04
Product high quality testing equipment
Systematic quality management team of 30 people, advanced testing equipment: physical tester, life tester, high precision inspection size tester, etc
STANDARDIZED PROCESSING FLOW
Relying on strong professional knowledge and a high-quality expert team, we provide customers with customized one-stop services for injection molding and mold development
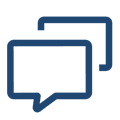
Demand Communication

01
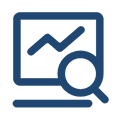
feasibility analysis

02
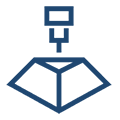
mold design

03
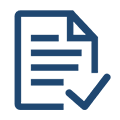
Customer Confirmation

04
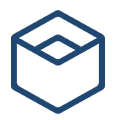
Mold manufacturing

05
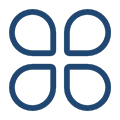
Sample delivery

06
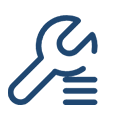
Internal optimization

07
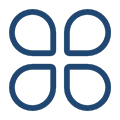
Sample delivery

08
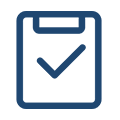
Customer Confirmation

09
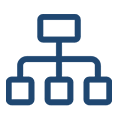
Mass production

10
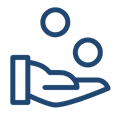
After-sales tracking

11
MORE PRODUCTS
PRODUCT CONSULTING
* Note: Please fill in the information accurately so as to facilitate smooth communication. We will contact you as soon as possible.