




ABS battery case
The ABS battery case is an important component of the battery. It serves to protect the internal battery pack, electronic components, and electrolyte, while also affecting the battery's durability, safety, and overall appearance.
Email:
The ABS battery shell is an important component of the battery, serving to protect the internal battery pack, electronic components, and electrolyte, while also affecting the battery's durability, safety, and overall appearance. Below is a detailed introduction to the ABS battery shell:
1. Characteristics of ABS Material
ABS (Acrylonitrile-Butadiene-Styrene) is a thermoplastic polymer material known for its high strength, good toughness, and ease of processing and molding. It has good moldability, resulting in products with a smooth surface that are easy to dye and electroplate. Additionally, ABS material can be blended with various resins to further enhance its performance.
2. Advantages of ABS Battery Shell
High strength and toughness: ABS material has high impact strength and toughness, effectively resisting external impacts and pressure to protect the internal battery pack from damage.
High-temperature resistance: Although ordinary ABS material may pose certain safety risks at high temperatures, flame-retardant ABS plastic has been modified to improve its high-temperature resistance, allowing it to withstand high-temperature environments without deformation or combustion within a certain range.
Chemical corrosion resistance: ABS material has good chemical corrosion resistance, able to withstand the erosion of electrolytes and other chemicals, extending the battery's lifespan.
Ease of processing and molding: ABS material can be easily processed into various shapes of shells through injection molding and other techniques to meet different design requirements for batteries.
3. Applications of ABS Battery Shell
ABS battery shells are widely used in various types of batteries, including automotive batteries, electric vehicle batteries, and energy storage batteries. Especially in the field of new energy vehicles, with the rapid development of electric and hybrid vehicles, the requirements for battery shells are also increasing. The excellent performance and cost-effectiveness of ABS battery shells make them an important choice in the new energy vehicle sector.
4. Production Process of ABS Battery Shell
The production process of ABS battery shells mainly includes injection molding and blow molding. Among these, injection molding is the most commonly used production method. The injection molding process has advantages such as high production efficiency, low cost, and strong adaptability. By optimizing injection molding process parameters and mold design, the production quality and performance of ABS battery shells can be further improved.
5. Maintenance and Care of ABS Battery Shell
Regular cleaning: Use a soft damp cloth to wipe the surface of the shell to remove dust and stains. Avoid using corrosive cleaners or sharp objects that could scratch the surface.
Avoid high-temperature environments: Try to place the battery in a cool, ventilated environment to avoid prolonged exposure to high temperatures that could cause deformation of the shell or damage to the internal battery.
Regular inspection: Regularly check for any damage, cracks, or deformation on the shell. If any abnormalities are found, replace the shell promptly to ensure safe use of the battery.
In summary, ABS battery shells possess excellent properties such as high strength, good toughness, high-temperature resistance, and chemical corrosion resistance, making them widely used in various batteries. By optimizing production processes and enhancing maintenance and care, the quality and performance of ABS battery shells can be further improved, extending the lifespan of batteries.
Classification:
Household appliance injection molds
Key words:
Household Appliances
Auto Parts
Medical Equipment
Deep branch in dongguan mould
Integration of mold manufacturing and molding production
ADVANTAGES
Development team adhering to the "customer first" service consciousness, relying on a strong professional knowledge and high quality expert team will develop its own position to provide customers with injection molding, mold development, customized one-stop service, meet customer's various customization development demand of professional team, to provide comprehensive solutions to the customers
01
Mold development, design and manufacture
Engineering development technical team size: 30 people.
02
Advanced modern precision mold equipment
62 high precision mold production equipment, the scale of 80 people.
03
Injection molding production
94 sets of injection molding equipment and 240 production personnel.
04
Product high quality testing equipment
Systematic quality management team of 30 people, advanced testing equipment: physical tester, life tester, high precision inspection size tester, etc
STANDARDIZED PROCESSING FLOW
Relying on strong professional knowledge and a high-quality expert team, we provide customers with customized one-stop services for injection molding and mold development
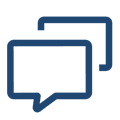
Demand Communication

01
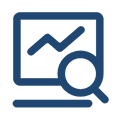
feasibility analysis

02
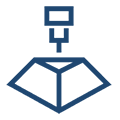
mold design

03
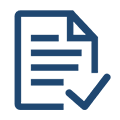
Customer Confirmation

04
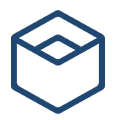
Mold manufacturing

05
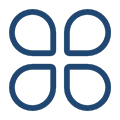
Sample delivery

06
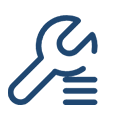
Internal optimization

07
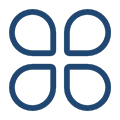
Sample delivery

08
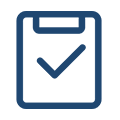
Customer Confirmation

09
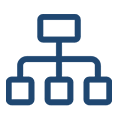
Mass production

10
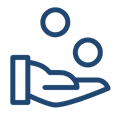
After-sales tracking

11
MORE PRODUCTS
PRODUCT CONSULTING
* Note: Please fill in the information accurately so as to facilitate smooth communication. We will contact you as soon as possible.