

Headphone plastic shell
Our headphone plastic shell is crafted from high-quality special engineering plastics. This material has excellent strength and toughness, effectively resisting collisions and scratches during daily use, while maintaining stable physical performance in extreme environments, ensuring reliable protection for the internal components of the headphones. In terms of design, it pursues ultimate ergonomics, fitting the contours of the ear, providing comfort and stability, and preventing any sense of pressure even during prolonged use. The surface of the shell is finely sanded, offering a delicate touch while effectively avoiding fingerprint residue, keeping the appearance neat and beautiful at all times. Its manufacturing process is exquisite, with precise stitching that not only enhances the overall aesthetics but also improves the product's sealing, effectively reducing sound leakage, allowing users to immerse themselves in a pure music world. In addition, the shell has good UV resistance, ensuring that long-term use does not lead to fading or aging issues, keeping it looking new.
Email:
Classification:
3C electronic headphone shell
Key words:
Integration of mold manufacturing and molding production
ADVANTAGES
Development team adhering to the "customer first" service consciousness, relying on a strong professional knowledge and high quality expert team will develop its own position to provide customers with injection molding, mold development, customized one-stop service, meet customer's various customization development demand of professional team, to provide comprehensive solutions to the customers
01
Mold development, design and manufacture
Engineering development technical team size: 30 people.
02
Advanced modern precision mold equipment
62 high precision mold production equipment, the scale of 80 people.
03
Injection molding production
94 sets of injection molding equipment and 240 production personnel.
04
Product high quality testing equipment
Systematic quality management team of 30 people, advanced testing equipment: physical tester, life tester, high precision inspection size tester, etc
STANDARDIZED PROCESSING FLOW
Relying on strong professional knowledge and a high-quality expert team, we provide customers with customized one-stop services for injection molding and mold development
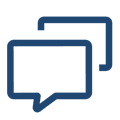
Demand Communication

01
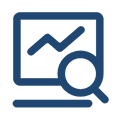
feasibility analysis

02
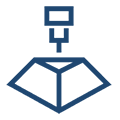
mold design

03
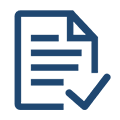
Customer Confirmation

04
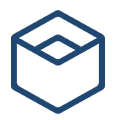
Mold manufacturing

05
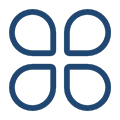
Sample delivery

06
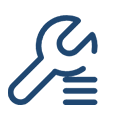
Internal optimization

07
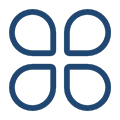
Sample delivery

08
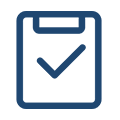
Customer Confirmation

09
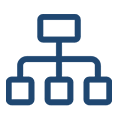
Mass production

10
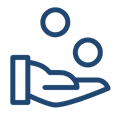
After-sales tracking

11
MORE PRODUCTS
PRODUCT CONSULTING
* Note: Please fill in the information accurately so as to facilitate smooth communication. We will contact you as soon as possible.