




Mini handheld wingless fan plastic shell
The plastic shell of the mini handheld wingless fan is an important component of the fan. It not only protects the internal structure of the fan but also determines the appearance and feel of the fan.
Email:
The plastic shell of the mini handheld bladeless fan is an important component of the fan. It not only protects the internal structure of the fan but also determines the appearance and feel of the fan. The following is a detailed analysis of the plastic shell of the mini handheld bladeless fan:
1. Shell Material
The plastic shell of the mini handheld bladeless fan is usually made of high-quality plastic materials, such as ABS plastic and PP plastic. These materials have good toughness, impact resistance, and chemical corrosion resistance, which can meet the strength and durability requirements of the fan shell. At the same time, these materials also have good processing performance, making them easy to mold and process.
2. Shell Design
Shape and Size: The design of the shell is usually determined based on the overall size and shape of the fan to ensure that the shell can tightly wrap around the internal structure of the fan. The shell of a mini handheld bladeless fan is usually compact, making it easy to carry and use.
Ventilation Design: Although the working principle of a bladeless fan differs from that of traditional fans, ventilation openings or ducts still need to be designed on the shell to ensure that air can flow smoothly through the fan and produce a cool breeze. These ventilation openings are usually carefully designed and optimized to achieve optimal ventilation effects and noise control.
Buttons and Indicator Lights: The shell will also be designed with control elements such as buttons and indicator lights, allowing users to easily control parameters such as turning the fan on or off and adjusting wind speed. These control elements are usually cleverly integrated into the shell to maintain a neat and aesthetically pleasing appearance.
3. Production Process
The plastic shell of the mini handheld bladeless fan is typically produced using injection molding technology. Injection molding is a process that involves injecting molten plastic into a mold and cooling it to solidify into a product. During production, it is necessary to select suitable injection molding machines and molds, as well as strictly control parameters such as injection temperature, pressure, and time to ensure the quality and dimensional accuracy of the shell.
4. Customization and Processing
Many manufacturers offer customization and processing services for plastic shells of mini handheld bladeless fans. Customers can choose parameters such as color, shape, and material of the shell according to their needs and preferences, and commission manufacturers for production and processing. These customization services typically include design of the shell, mold manufacturing, injection molding, and subsequent processing stages to meet customers' personalized needs.
5. Price and Suppliers
The price of plastic shells for mini handheld bladeless fans varies based on factors such as material, design, production process, and degree of customization. On e-commerce platforms like Alibaba 1688, many suppliers and manufacturers offering such shells can be found. These suppliers usually provide different specifications and models for customers to choose from, and can customize and process according to customer needs. In terms of price, due to market competition and supply-demand relationships, prices may fluctuate. Therefore, when selecting suppliers and purchasing shells, it is recommended that customers conduct comprehensive comparisons and evaluations to choose products with the best cost-performance ratio.
In summary, the plastic shell of a mini handheld bladeless fan is an important component of the fan. Factors such as material, design, production process, and degree of customization will affect the quality and performance of the fan. When selecting and purchasing shells, it is recommended that customers choose based on their needs and preferences while paying attention to the quality and durability of the shell.
Classification:
Household appliance injection molds
Key words:
Household Appliances
Auto Parts
Medical Equipment
Deep branch in dongguan mould
Integration of mold manufacturing and molding production
ADVANTAGES
Development team adhering to the "customer first" service consciousness, relying on a strong professional knowledge and high quality expert team will develop its own position to provide customers with injection molding, mold development, customized one-stop service, meet customer's various customization development demand of professional team, to provide comprehensive solutions to the customers
01
Mold development, design and manufacture
Engineering development technical team size: 30 people.
02
Advanced modern precision mold equipment
62 high precision mold production equipment, the scale of 80 people.
03
Injection molding production
94 sets of injection molding equipment and 240 production personnel.
04
Product high quality testing equipment
Systematic quality management team of 30 people, advanced testing equipment: physical tester, life tester, high precision inspection size tester, etc
STANDARDIZED PROCESSING FLOW
Relying on strong professional knowledge and a high-quality expert team, we provide customers with customized one-stop services for injection molding and mold development
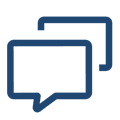
Demand Communication

01
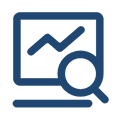
feasibility analysis

02
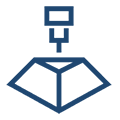
mold design

03
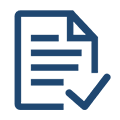
Customer Confirmation

04
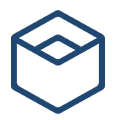
Mold manufacturing

05
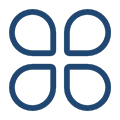
Sample delivery

06
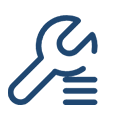
Internal optimization

07
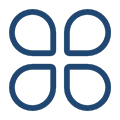
Sample delivery

08
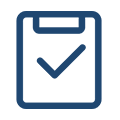
Customer Confirmation

09
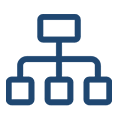
Mass production

10
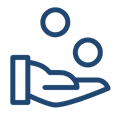
After-sales tracking

11
MORE PRODUCTS
PRODUCT CONSULTING
* Note: Please fill in the information accurately so as to facilitate smooth communication. We will contact you as soon as possible.